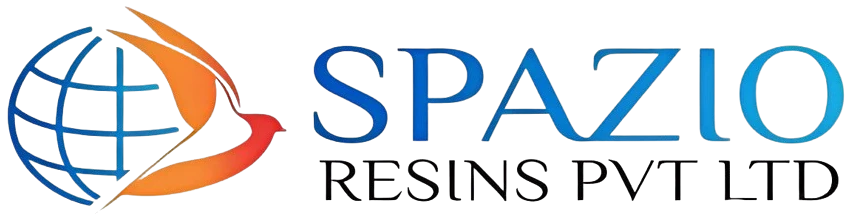
About Polymer
At Spazio Resins, we are dedicated to pioneering innovative and sustainable resin solutions for industries worldwide. With a strong commitment to quality, performance, and environmental responsibility, we provide advanced thermoplastic resins tailored to meet the evolving needs of our customers.
Our expertise spans recyclable and recycled resins, lightweight solutions, bio-based alternatives, and eco-friendly compounding processes, ensuring that our products contribute to a greener future. We believe in responsible manufacturing, incorporating low-impact additives, waste reduction programs, and energy-efficient processes to minimize our environmental footprint.
Beyond our products, Spazio Resins actively supports corporate social responsibility (CSR) initiatives, fostering positive impacts on communities, employees, and the environment. Our mission is to enable sustainable innovation, helping businesses transition to more responsible material choices without compromising on performance.
Products Offering
ABS (Acrylonitrile Butadiene Styrene)
Properties: High impact resistance, toughness, gloss, and excellent dimensional stability. Can be easily colored and has good chemical resistance, especially to acids and alkalis.
Uses: Widely used in automotive parts like dashboards and bumper components, electronic casings, consumer electronics (keyboard keys, printer parts), and toys (e.g., LEGO bricks).
Advantages: Good impact resistance, rigid structure, easy to machine and mold, and capable of withstanding high-stress applications.
ASA (Acrylonitrile Styrene Acrylate)
Properties: UV stability, high impact resistance, weather and chemical resistance, excellent gloss, and durability in high and low temperatures.
Uses: Suitable for outdoor applications such as automotive trims, siding, outdoor furniture, and sports equipment.
Advantages: Superior weather resistance, good color stability, impact resistance, and strong resilience to fading or yellowing from sunlight.
SAN (Styrene Acrylonitrile)
Properties: Clarity, stiffness, good chemical resistance, and better thermal resistance than polystyrene.
Uses: Common in food storage containers, cosmetic packaging, and laboratory equipment. SAN is also used for making kitchenware, toothbrushes, and syringes.
Advantages: High transparency, ease of processing, rigidity, and resistance to oils and other chemicals.
HIPS (High Impact Polystyrene)
Properties: High impact resistance, easy to process, good machinability, and moderate strength.
Uses: Often used for low-cost, single-use products like disposable cutlery, cups, toys, and packaging.
Advantages: Easy to process, economical, good impact strength, and lightweight.
GPPS (General Purpose Polystyrene)
Properties: High clarity, low cost, and good rigidity.
Uses: Common in packaging, CD and DVD cases, clear food containers, and cosmetic jars.
Advantages: Good optical clarity, rigidity, and low cost. However, it is brittle and may crack under high impact.
TPU (Thermoplastic Polyurethane)
Properties: High elasticity, flexibility, abrasion resistance, and impact strength.
Uses: Footwear, cable jackets, flexible tubing, conveyor belts, and protective cases for electronic devices.
Advantages: Great abrasion resistance, flexibility, and resilience. Retains elasticity over a wide temperature range.
K-Resin (SBS Copolymer)
Properties: High clarity, good impact resistance, lightweight, and resistant to breakage.
Uses: Packaging, clear displays, medical packaging, and consumer goods.
Advantages: Superior clarity, toughness, and easy processing.
Transparent ABS (MABS)
Properties: Clear, tough, and impact resistant, with good color ability.
Uses: Transparent cases, medical devices, cosmetic packaging, and toy applications.
Advantages: Good transparency, impact strength, chemical resistance, and aesthetic appeal.
Polyacetal (POM)
Properties: High stiffness, strength, low friction, wear resistance, and good dimensional stability.
Uses: Gears, bearings, fasteners, precision components, automotive fuel systems, and zippers.
Advantages: Excellent wear resistance, high strength, low moisture absorption, and chemical resistance.
Polyamides (Nylon 6, 66, 6/12, 10, 11)
Properties: High strength, flexibility, durability, wear and chemical resistance.
Uses: Automotive components, gears, bearings, textiles, industrial parts, and sportswear.
Advantages: High mechanical strength, flexibility, chemical resistance, and good performance in high-stress applications.
PBT (Polybutylene Terephthalate)
Properties: High rigidity, low moisture absorption, electrical insulation, and good chemical resistance.
Uses: Electrical connectors, automotive parts, small appliance housings, and electronics.
Advantages: Dimensional stability, low warping, chemical resistance, and durability.
PMMA (Polymethyl Methacrylate)
Properties: High clarity, UV resistance, and lightweight.
Uses: Lenses, windows, signage, displays, and aquariums.
Advantages: High transparency, good weatherability, scratch resistance, and lightweight.
Polycarbonate
Properties: High impact resistance, thermal stability, and transparency.
Uses: Eyewear lenses, security glazing, bulletproof windows, medical devices, and electronics casings.
Advantages: Excellent toughness, optical clarity, thermal stability, and lightweight.
PVC (Polyvinyl Chloride)
Properties: Durability, chemical resistance, and fire resistance.
Uses: Piping, flooring, medical tubing, cable insulation, and inflatable products.
Advantages: Cost-effective, durable, resistant to weathering and chemicals.
EVA (Ethylene Vinyl Acetate)
Properties: Softness, flexibility, lightweight, and resistance to water.
Uses: Foam materials, footwear soles, sports padding, and medical devices.
Advantages: Lightweight, flexible, water resistance, and high resilience.
COMPOUNDS INFORMATION
Properties: Excellent impact resistance, thermal stability, and rigidity.
Uses: Automotive components, electronics housings, and consumer goods.
Advantages: Good balance of strength, toughness, and dimensional stability.
Properties: High chemical resistance, good impact strength, and thermal stability.
Uses: Automotive parts, electrical connectors, and housings.
Advantages: Chemical resistance, toughness, and dimensional stability.
Properties: High impact resistance, improved thermal stability, and better dimensional stability.
Uses: Automotive parts, electronics, and industrial applications.
Advantages: Durable, resistant to impact, and stable at high temperatures.
Properties: Excellent dimensional stability, impact resistance, and heat resistance.
Uses: Electrical connectors, automotive components, and consumer electronics.
Advantages: Chemical resistance, thermal stability, and mechanical strength.
Properties: Good dimensional stability, toughness, and weather resistance.
Uses: Automotive parts, electronic components, and appliance housings.
Advantages: Good balance of impact strength, chemical resistance, and toughness.
Properties: High UV and weather resistance, impact strength, and good aesthetic properties.
Uses: Outdoor products, automotive trims, and equipment casings.
Advantages: High durability, UV stability, and excellent impact resistance.
Properties: High chemical resistance, impact strength, and reduced density.
Uses: Automotive and industrial components where lightweight and durability are important.
Advantages: Lightweight, chemically stable, and impact resistant.
Properties: High mechanical strength, impact resistance, and chemical durability.
Uses: Electrical enclosures, automotive parts, and industrial applications.
Advantages: Excellent impact and chemical resistance, and enhanced mechanical properties.
Properties: Improved lubricity and reduced wear.
Uses: Bearings, gears, and other mechanical components.
Advantages: Self-lubricating properties that extend part life and reduce maintenance.
Properties: Higher tensile strength (GF) and resistance to ignition and flame spread (FR).
Uses: Automotive parts, electronics, construction, and appliances.
Advantages: Increased structural strength and fire safety for critical applications.
Processing Conditions Guide For Polymers
Polymer Type | Melt Temp (°C) | Mold Temp (°C) | Drying Temp (°C) | Hours | Dew Point (°C) | Moisture Content (%) |
---|---|---|---|---|---|---|
PP(Polypropylene) | 191-232 | 32-66 | 79 | 2 | n/a | 0.10 |
PA (Nylon 6/6) | 277-299 | 66-107 | 79 | 2 to 4 | -18 | 0.20 |
PA (Nylon 6) | 243-299 | 54-93 | 79 | 2 to 4 | -18 | 0.20 |
PA (Nylon 6/10) | 277-299 | 66-107 | 79 | 2 to 4 | -18 | 0.20 |
PA (Nylon 11) | 249-285 | 60-93 | 79 | 4 | -18 | 0.20 |
PA (Nylon 6/12) | 249-285 | 60-93 | 79 | 4 | -18 | 0.20 |
PA (Amorphous Nylon) | 271-299 | 66-99 | 79 | 4 | -34 | 0.20 |
PA (Nylon 12) | 221-274 | 66-104 | 79 | 4 | -40 | 0.10 |
PA (Impact-Modified Nylon 6/6) | 277-299 | 66-107 | 79 | 2 to 4 | -18 | 0.20 |
PARA (Polyarylamide) | 271-279 | 121-144 | 80 | 12 | -18 | 0.20 |
PC (Polycarbonate) | 288-216 | 82-121 | 80 | 4 | -29 | 0.20 |
PS (Polystyrene) | 210-249 | 38-66 | 82 | 2 | n/a | n/a |
SAN (Styrene Acrylonitrile) | 238-279 | 52-82 | 82 | 2 | n/a | n/a |
ABS (Acrylonitrile Butadiene Styrene) | 204-238 | 63-85 | 82 | 2 | -18 | 0.10 |
HDPE (High Density Polyethylene) | 193-232 | 21-66 | 79 | 2 | n/a | n/a |
LDPE (Low Density Polyethylene) | 193-232 | 21-66 | 79 | 2 | n/a | n/a |
POM (Acetal) | 182-218 | 82-121 | 79 | 2 to 4 | -32 | 0.15 |
PSU (Polysulfone) | 332-271 | 93-149 | 135 | 4 | -32 | 0.15 |
PBT (Polybutylene Terephthalate) | 238-271 | 66-121 | 121 | 4 | -29 | 0.03 |
PET (Polyethylene Terephthalate) | 260-298 | 135-163 | 121 | 4 | 40 | 0.01 |
TPUR (Ester-based Thermoplastic Polyurethane Elastomer) | 171-218 | 38-60 | 107 | 6 | -18 | 0.01 |
PPS (Polyphenylene Sulfide) | 307-329 | 135-177 | 149 | 6 | n/a | 0.02 |
PMMA (Acrylic) | 204-249 | 79-107 | 79 | 4 | -20 | 0.02 |
PC/PMMA (Polycarbonate / Acrylic Alloy) | 238-266 | 32-66 | 82 | 4 | -28 | 0.02 |
PC/ABS (PC/ABS Alloy) | 243-274 | 52-93 | 93 | 4 | -29 | 0.02 |
PMP (Polymethylpentene) | 266-304 | 66-93 | 79 | 2 | n/a | n/a |
LCP (Liquid Crystal Polymer) | 332-366 | 66-121 | 149 | 8 | -29 | 0.02 |
FEP (Fluorinated Ethylene Propylene) | 343-385 | 96+ | 121 | 2 to 4 | n/a | n/a |
PPA (Polyphthalamide) | 302-329 | 135-163 | 79 | 6 | -32 | -0.05 |
TPI (Thermoplastic Polyimide) | 399-416 | 177-232 | 204 | 8-10 | -40 | -0.01 |
PSU/PC (Polysulfone/Polycarbonate Alloy) | 282-327 | 66-99 | 121 | 4 | -29 | -0.02 |
Spazio Resins
+91- 8010777754